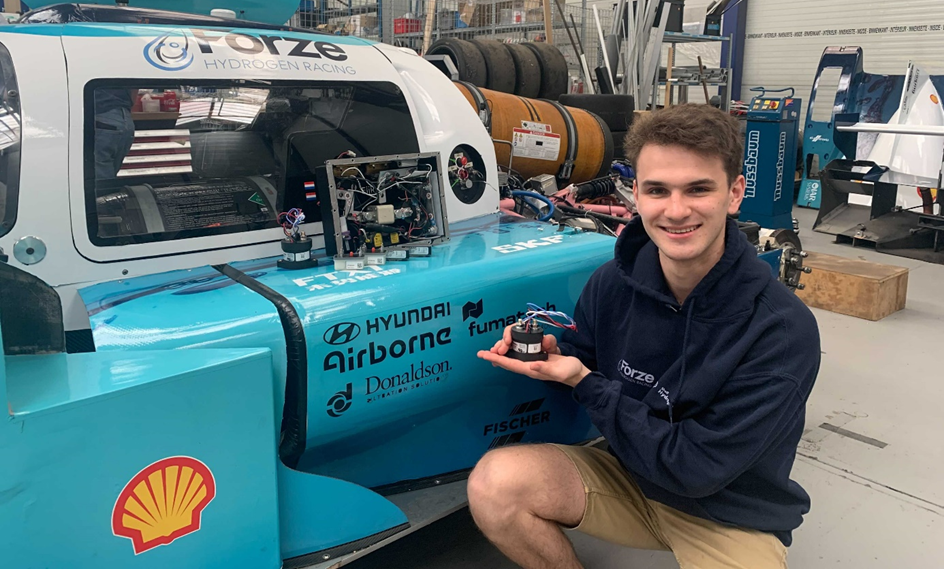
The Forze Hydrogen Racing Team is about to start assembling the Forze IX. The Forze IX is to become the world’s fastest hydrogen race car. The new hydrogen electric race car can go from 0 to 100 km/h in just 3 seconds and can reach a top speed of 300 km/h. The greater purpose is to show that hydrogen is a good alternative to fossil fuels. We talked with Chief Powertrain Bob Morssink about the new design, the impact of Covid-19, the lack of availability in components and the Gigavac relays and contactors delivered by Nijkerk Electronics.
Racing at circuit Zandvoort and the TT circuit in Assen
To show the actual speed of the car, the team wants to participate in the Supercar Challenge (at the circuit at Zandvoort and the TT circuit in Assen among others). To be able to win in this challenge, the car is built in different stages.
Bob: “First we will drive the car with only rear wheel drive, one fuel cell and corresponding components. If the car appears to be reliable with only these parts, the next goal is to install a second fuel cell, together with front wheel drive. If this is successful, we will be ready to participate for the win at GT level.”
The biggest challenges: Covid-19 and lack of available components
Normally, the biggest challenge for the team is to create a faster and better car than its predecessor. This team had completely different challenges.
Bob: “The situation with Covid-19 made us work from home. This caused the project some delays and team bonding was harder this year. Despite the fact we couldn’t work at the same location, the motivation in the team was still very strong. Then there was the lack of components. We had to order most of the Integrated Circuits (ICs) and other components for PCBs in advance. Because of the advanced orders, we have less freedom to design the PCBs. Normally, components are ordered after the electrical circuit designs are finished. This means we can implement changes in the design of the PCB at a later moment.”
“This summer we can finally start building the car. Then there will be a long period of testing, to make sure we can get maximum performance from the car. We expect to present the new car around November.”
Most important enhancements of Forze IX
Despite all these challenges, the team has succeeded to implement important enhancements in the design. The biggest change is the doubling of power.
Bob: “The first enhancement to the car is the building of two Balance of Plants (BoP) instead of one. A BoP consists of a fuel cell and the system necessary to get the air and the hydrogen in the best condition before it enters the fuel cell. Two BoPs means we have twice the power to drive the car.”
“The second significant enhancement is the completely redesigned embedded system. The new design processes all data in one central place, in this case, the Central Processing Stack (CPS). Data collection is done by the Distributed Interfacing Nodes (DINs). These nodes are pieces of identical hardware and can be programmed in the software. Therefore, the DINs can be exchanged in the car without crashing the system. This creates a flexible system, which is very necessary, because the car has more than 400 sensors and actuators.”
Gigavac components by Nijkerk Electronics
Nijkerk Electronics has contributed three Gigavac components to the design. Bob explains why these components were chosen and how they are used.
GV241CAB: These contactors are used in our junction boxes to disconnect the car’s high voltage system from the fuel cells and the accumulator. When the fuel cells and the accumulator are disconnected, the high voltage system is discharged, so our engineers can work at the system safely. We chose the GV241CAB because of its high performance and because of their compactness and light weight. These are important characteristics for a race car.
P125CDA: The P125CDA contactors are used to connect the high voltage system to the converters. These converters change high voltage to low voltage which provides power to the embedded systems. The P125CDA is chosen because it can handle voltages up to 1200V, has a low contact resistance and only weighs 90 grams.
G81C335: The G81C335 is the same as the other two components: it is a lightweight relay which can resist high voltages and can conduct the correct amount of current.
For more information: